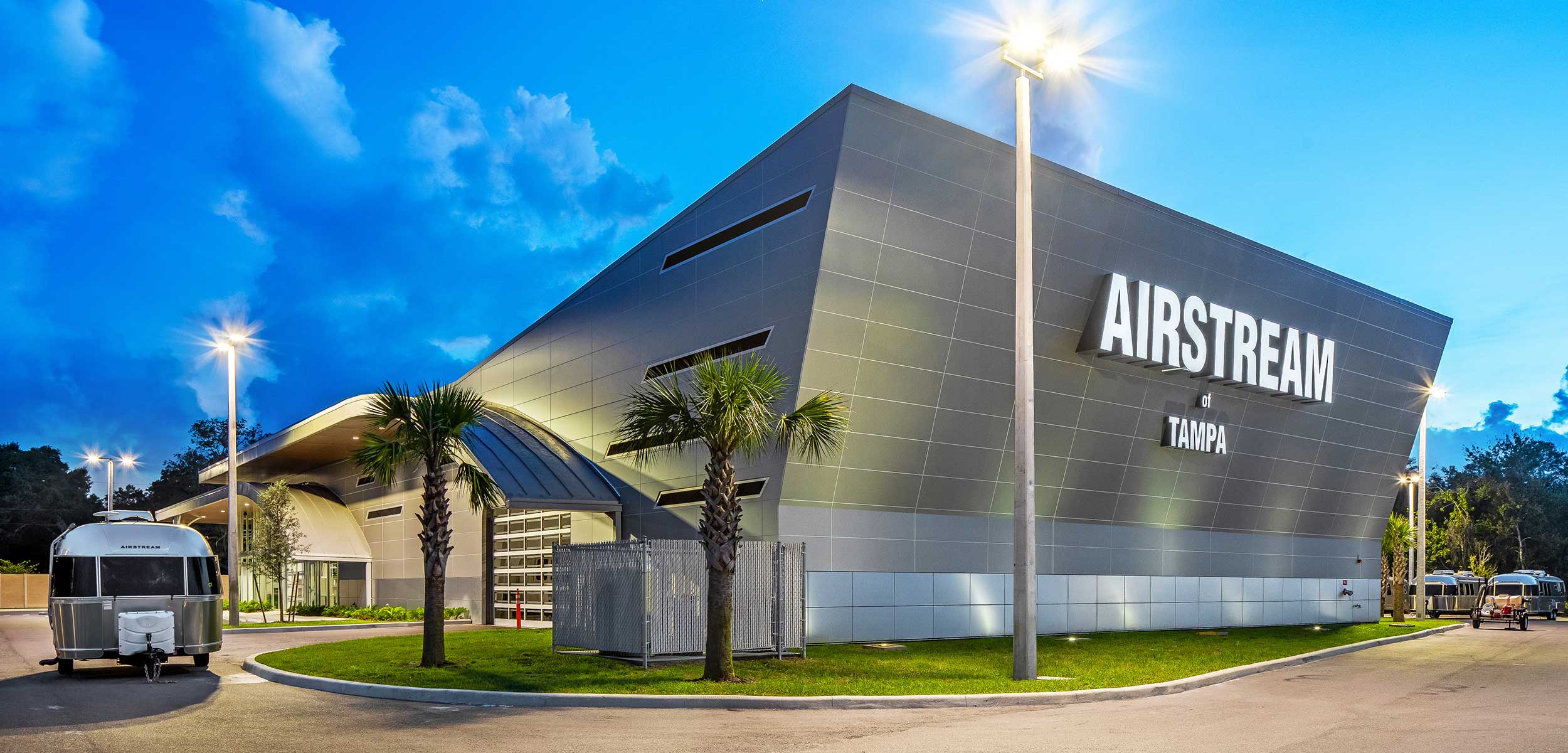
Cuhaci Peterson worked with Airstream of Tampa, now a part of Thor Industries, Inc., to deliver a state-of-the-art facility to showcase its powerful brand which opened its doors in 2018.
The facility, “World’s Largest Airstream Dealership” located in Dover, Florida (near Lakeland and in between Orlando and Tampa), was designed with a subtle nod to the iconic shiny aluminum shell of the Airstream itself, but with classic and sharp contemporary lines. Visitors of the facility will find all makes and models of Airstream as well as a complete museum-like display of Airstream history and a gift shop. In addition, visitors will see a 360-degree movie theater where guests are immersed into a guided tour of the manufacturer’s production facility in Jackson Center, Ohio.
The unique experience offers enthusiasts a behind the scenes look at actual employees assembling Airstreams as well as a shell model on site to show how their products are made. Airstream of Tampa was named 2022 top overall U.S. Airstream dealership, with the highest sales for towable and motorized combined at an individual location as well as the #1 Airstream dealership in the world from 2020-21. These legendary travel trailers and touring coaches have been on the roads more than 90 years and chances are, you’ve seen them many times in your travels.